2024 was the year of cautious optimism for homeowners and pros when it came to willingness to start home improvement projects and 2025 is currently shaping up similarly from the results we're seeing through the market research we conduct quarterly.
As we’ve done for the last 4 years, The Farnsworth Group and The Home Improvement Research Institute have studied the activities and sentiments of homeowners and pros on a quarterly basis through the Quarterly Homeowner Activity Tracker and the Quarterly Contractor Activity Tracker.
Below, we want to highlight a few areas of interest we believe are important to you and your organization for improving your go-to-market strategies in 2025.
In the Eyes of Trade Professionals
Despite inadequate job growth for the industry and slower project activity over the recent couple of years as we came off the heels of the pandemic, tradesmen are continuing to be optimistic about growth in the home improvement market and business revenue over the next year. Roughly 3 in 4 tradesmen are projecting revenue increases in 2025, and stated their greatest opportunities for business growth were in expanding current service offerings as well as investing in new technology.
Consistent through 2024, about half of tradesmen reported an increase across their various activities versus quarter over quarter. Additionally, there were fewer contractors (26%) in Q4 of 2024 state that they were forced to cancel or postpone a project and when there was a need to cancel a project the top drivers were the homeowner’s decision, a schedule/timing reason, or due to material availability.
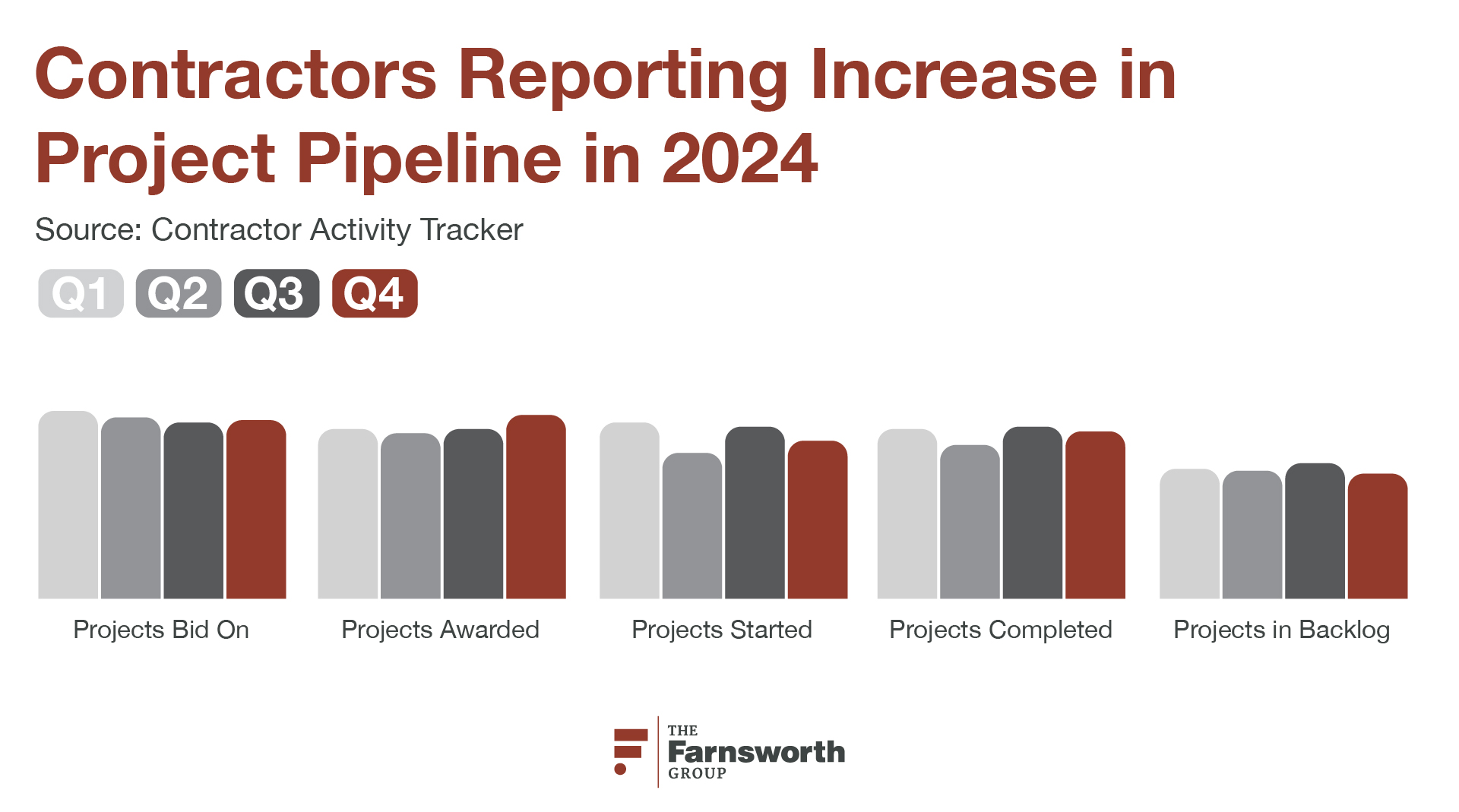
However, while there is optimism for growth potential in 2025, tradesmen are seeing their greatest challenges for growth being material shortages, a lack of labor, increasing competition. Labor in particular has several components that are magnifying the issue even further—not only is there a large concern on labor availability (with 61% of tradesmen stating that), the cost of that labor and more importantly the quality of the labor is a major concern—with a continuing need of more tradesmen to enter the profession, when a Boomer is retiring from the craft, the number of experienced and seasoned tradesmen shrinks even further.
It is encouraging that there is optimism among tradesmen as we enter 2025. While tradesmen face many obstacles there is reason for hope, especially as 2025 progress and 2026 begins. Those smaller DIY projects that were completed during the pandemic have likely dried up some need for those in 2025, so look to see contractors engaging on a higher number of bigger projects, like kitchen remodels, that are too daunting for they typical DIYer to tackle. Only time will tell how the lack of skilled labor impacts that increased need for more complicated projects.
In the Eyes of Homeowners (DIY and DIFM)
In order to access the DIY market, it’s important to understand its demographics, as well as the motivations, behaviors and trends influencing different groups within the market. Let’s unpack this group of home improvement product buyers.
DIY Home Improvement Trends and Statistics
U.S. homeowners have been active in their home projects especially as we progressed into the back half of the year. Homeowner focus in Q4 of last year was more towards home maintenance and repair projects, and as winter settled in there was less motivation for larger discretionary projects like home renovations
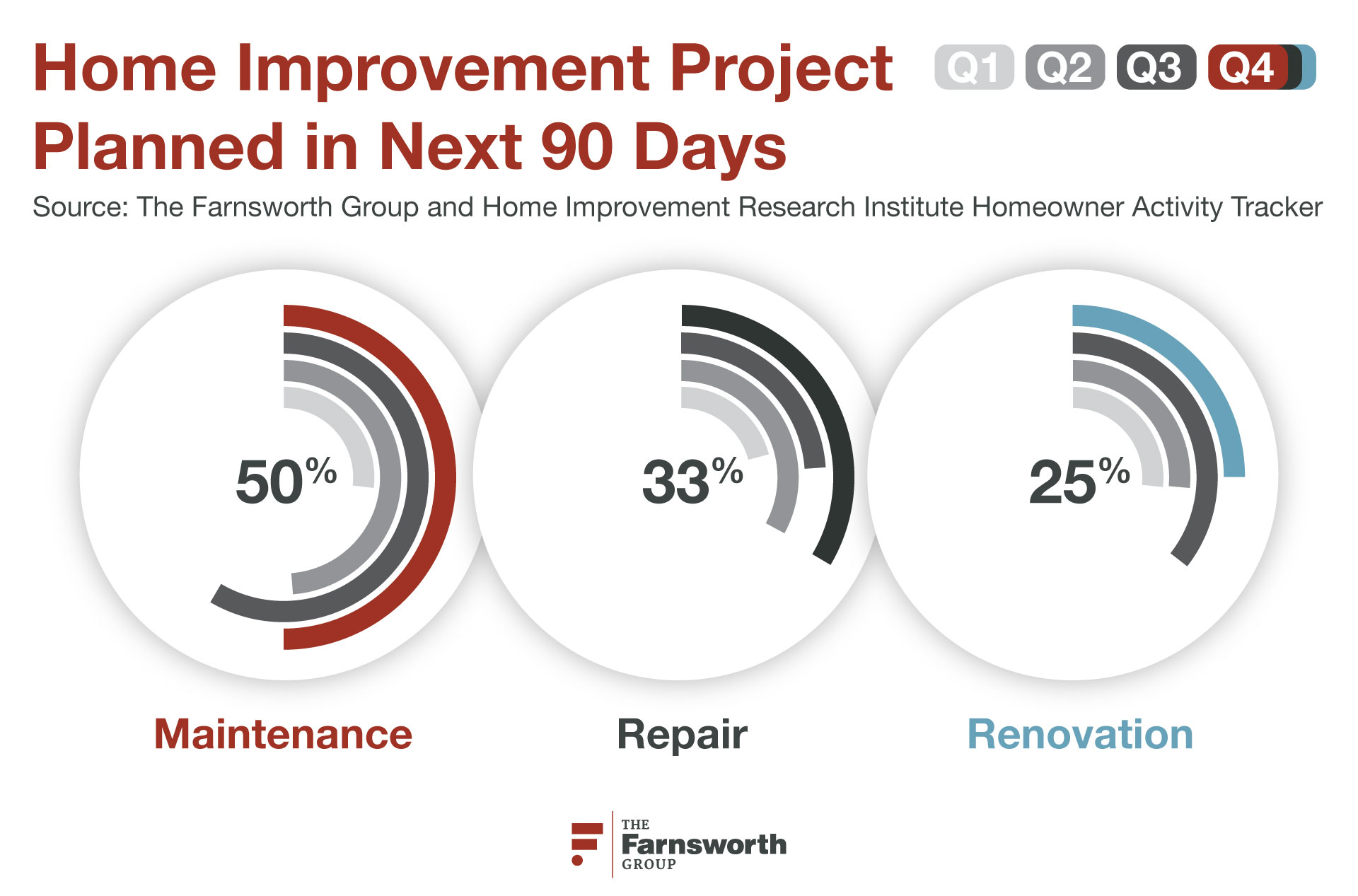
During Q4, 41% of homeowners completed some sort of home improvement, repair, or maintenance project. Primarily, projects undertaken were routine maintenance (82% completing this type of project) or fixing damaged areas of the home (70%). Even though these types of projects are not always large ticket items, homeowners did spend more money and more time on these projects in Q4, especially compared to Q2 and Q1.
With 55% of homeowners completing a project fully themselves, these DIYers continue to be driving by pricing—as it is simply cheaper for them to tackle these projects than to hire out a pro. As 2025 and 2026 evolve it will be important to continue to keep a pulse on homeowners as labor challenges are expected to continue to get worse. This contractor labor strain may cause some homeowners to become reluctant DIYers in order for their projects to simple be completed with some semblance of timeliness.
“And as we’ve said time and time and time again, pay attention to that project intent, because it is a great leading indicator of what retail home improvement sales may be,” said Farnsworth. “Dig deep into your product and the related projects to understand where those opportunities may lie for your organization.”
Looking Ahead to Customer Behaviors in 2025
These broader trends reveal how the home improvement market progressed throughout the year. But what about your customers specifically? Our dive into tactics for increasing market penetration describes how go-to-market strategies tailored to your customers can increase sales and profit margins. This all starts with getting a deep understanding of your customer, their purchase drivers, and how they compare options when making a purchase decision. You can secure this knowledge through custom usage and attitude market research.
Our market research firm provides building product manufacturers and suppliers with customized research specific to their needs to better understand DIYers. We also provide the industry with a pulse on DIYer sentiments and through our annual Building Products Customer Guide. This data can help you look forward to how the home improvement industry is likely to evolve—and how it will stay the same—in the coming years.
Written By Taylor Pence
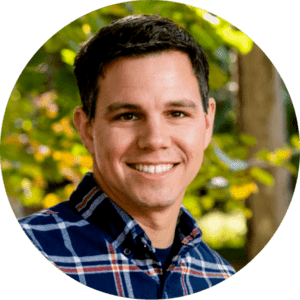
Taylor has been serving clients and managing quantitative market research studies with The Farnsworth Group since 2015. Taylor also supports internal team development and training efforts to ensure the research team at The Farnsworth Group is current on best practices and equipped to deliver on high standards.
Taylor’s interest in the home improvement space began when he was about 10 years old upon discovery of ‘This Old House’ and Norm Abram’s ‘ New Yankey Workshop.’ Fast-forward a couple of decades and he still enjoys these sources of inspiration while tackling the perils of DIY in his own workshop. Taylor is proud husband to Lauren, and father to three awesome kids. Whenever possible, Taylor shares his hobbies with his kids, including playing music, tennis, golf, going fishing or putting his hands to a new project in the shop.